Historically, saggars were used to protect glazes and wares from the open flame, gases, and ash inherent in the process of wood-firing. This technique was used in ancient China, Korea, Japan, and even the later industrial potteries of Great Brittain. The name itself derives from a contraction of "safeguard". Saggars were constructed of large clay jars or brick boxes placed inside the kiln.
Contemporary potters use saggars in a way completely opposite to the original use intended. Instead of placing a pot in an empty saggar for protection, potters intentionally fill it up with all kinds of "gunk". Organic materials, such as banana peels, cat food, leaves, and twigs can be attached to the vessel with copper wire, masking tape, steel wool, etc. This concoction can be further covered with sawdust, salt, baking soda, copper carbonate, red iron oxide, newspaper-- you name it. The possibilities are endless with any number of the ingredients listed above as well as a myriad of other choices.
I was taught to saggar fire in an outdoor raku kiln by applying some of the above ingredients and then wrapping the entire thing in tin foil. The pots were fired until they "looked right" (about 1400 degrees) at which point they were pulled out, unwrapped, and put in water to cool.
When reintroduced to saggar at another college, I found that the method practiced was completely different. Pots were still wrapped in combustibles and organic material, but then they were wrapped in a newspaper bundle. This bundle was then loaded in a box built of firebrick inside an outdoor gas kiln. The space around the pots was filled with pine needles, sawdust, salt, copper sulfate, and red iron oxide and sealed on top with a kiln shelf. This was fired to between 1600 and 1799 degrees and allowed to cool for several days before emptying.
Intrigued by the difference in techniques and the range of possibilites, I started researching saggar firing. I found some great online resouces in Wanda Garrity , who was quick to answer my questions about her techniques through emails, Dick Lehman's site, which has a good article about a method for getting carbon imprints, and Pitfire, Matt Hoogland's personal website that has a lot of information about saggars and terra sigilata. Barrel, Pit, and Saggar Firing by Sumi Von Dassow has been a great reading resource. It is a collection of Ceramics Monthly Articles about the topic. Another good read, which was reccomended to me by Wanda Garrity, is Alternative Kilns & Firing Techniques.
Yesterday, I tested out a new method (to me--I'm sure someone, somewhere has done it before) created from a combination of past experience and reading.
After painting on a layer of ferric chloride, I wrapped my pots in organics (ok, so I cleaned out my fridge and ended up using moldy peppers and broccoli), copper scrubbing pads, and sawdust with a pinch of salt and some copper carbonate. This package was then wrapped in tin foil with the shiny side out. All of the tin foil packs were tumble-stacked in my electric kiln and fired to cone 18--about 1390 degrees.
The results were not what I had expected. The sawdust only blackened the ware where there was a lot of it in intimate contact. The organics and copper scrubbers burned out a pale orange/pink. For the next firing, I think that I will use more sawdust in more concentrated areas. Also, right after firing, I read in Alternative Kilns & Firing Techniques that salt can corrode the elements in an electric kiln. So, no more salt in the next firing--I'm lucky that I didn't put much in the last one. But copper carbonate, red iron oxide, and other colorants are still fair game. I'm also thinking of experimenting with pit firing in my inlaw's backyard (large) fire pit.
Below are two examples of saggar fired pots. The first was fired at the college lab in a gas kiln, the second was fired in my electric. To see more of my finished saggar pots, check out my website TRPottery.
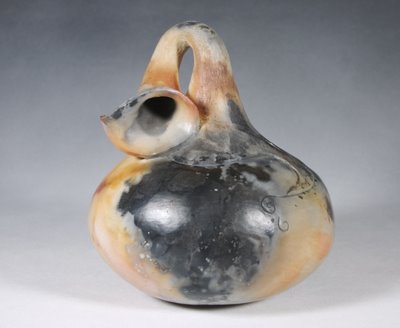
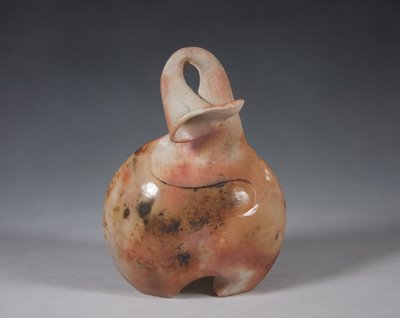
4 comments:
Saw your blog and thought I would comment to give you some ideas. This woman: http://lisaluera.deviantart.com/gallery/#Foil-Saggar uses sugar instead of salt and her results are amazing. I believe she also uses the ferric chloride and some horse hair, etc.
Good luck and have fun potting!
Sugar produces small isolated white spots that can look interesting. Very much the reverse of what it does on a horse hair peice. Copper tends to produce dark black carbon spots which can get really interesting if the wire is thin enough. Thick wire produces really significant dark black areas that tend to distract from the finish.
I wonder what coal or charcole dust would do.
After you fire the peice, do you apply anything to it to seal or protect the very delicate finish?
I really like when people are expressing their opinion and thought. So I like the way you are writing
I find the creative possibilities within saggar firing to be very exciting.
Post a Comment